decarbSTEEL: From classroom to conference debut
Giordana Verrengia
May 8, 2025
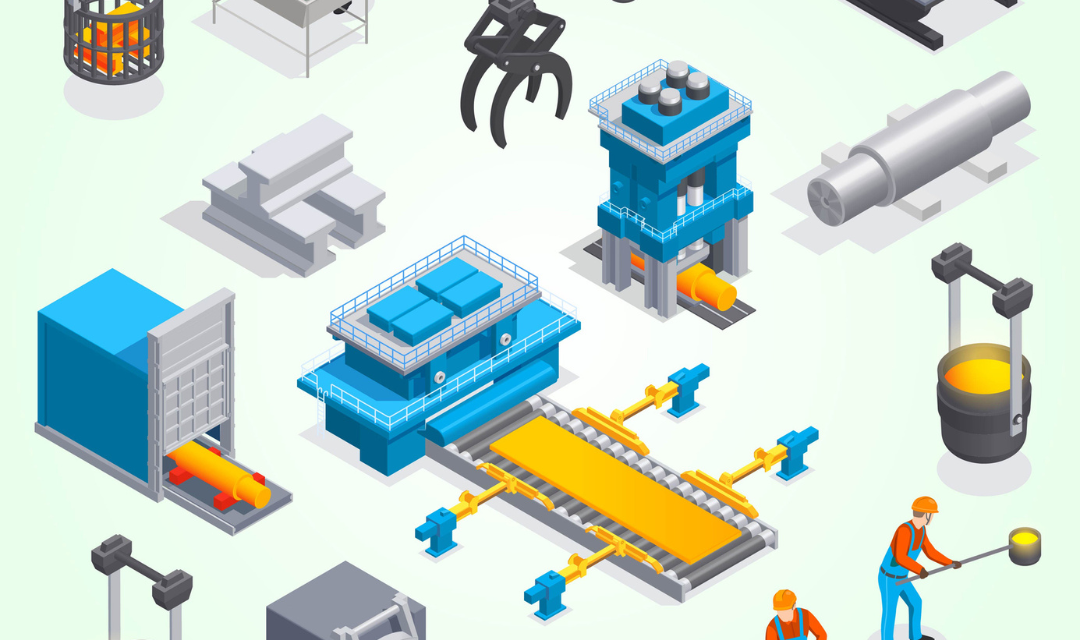
Thanks to a Sustainable Technologies for Steel Manufacturing Grant from the Association for Iron and Steel Technology (AIST), Carnegie Mellon researchers spent the spring semester developing decarbSTEEL (Decarbonizing Steelmaking TechnoEconomic EvaLuation), an open-source, highly customizable Excel-based framework for assessing the cost and carbon dioxide (CO2) emissions of different steel decarbonization strategies.
The faculty leads were Chris Pistorius, co-director of the Center for Iron and Steelmaking Research (CISR); and Valerie Karplus, associate director of the Scott Institute for Energy Innovation.
Much like the annual Accelerating Green Steel Workshop, decarbSTEEL is another CISR-Scott Institute joint initiative to support decarbonization in the iron and steel industry. Whereas the workshop gathered global representatives to take stock of sustainability in the industry, decarbSTEEL is an open-access resource that makes it easy to crunch the numbers and choose design pathways for iron and steel production that are both financially viable and sustainable.
“All calculations run in Excel, using open source, easily accessible data to keep the tool transparent and user-friendly,” said project manager Elina Hoffmann, a postdoctoral research associate in engineering and public policy. “Many assumptions are customizable – for example, you can simply change the electricity source using a dropdown menu to see how switching to CO2-free electricity affects production costs and CO2 emissions intensity.”
decarbSTEEL provides essential information for companies and government policymakers when determining whether or not to invest in various technology options for making steel with lower or near-zero CO2 emissions, Karplus explained.
“The tool not only helps decision makers understand the cost and CO2 emissions tradeoffs across different iron and steelmaking pathways, but also explore design decisions within each one,” said Hoffmann. “For instance, within the hydrogen-based direct reduced iron-electric arc furnace (DRI-EAF) steelmaking pathway, users can select hydrogen production methods and preheating strategies in the model.”
After a semester of testing, training, and refining the model, decarbSTEEL made its conference debut at AISTech 2025 in Nashville. Hoffmann presented the team’s work in a technical session, and the student researchers submitted posters about their individual contributions to the model, including the addition of mass-and-energy-balances; kinetic models; industry averages; and other factors that boost the comprehensiveness of decarbSTEEL’s cost and CO2 emissions figures.
The team benefited from regular interaction with the project’s industry mentors at United States Steel Corporation and Steel Dynamics, Inc. Students underscored the value of being able to work across disciplines to develop a tool of real, practical value to the industry.
“Attending AISTech provided a valuable opportunity to gain insights into the overall trends shaping the steel industry and to bridge our academic work with the industry’s priorities,” said Bright Aungsuthar, a master’s student in civil and environmental engineering. “The experience made me realize that our work has the potential to spark real change in the industry.”
Other contributors to the model development team included Emily Allendorf, En Hung, Shashank Swaminathan, Albert Chang, Adwait Joshi, and Yucheng Zhang.
The decarbSTEEL tool can be downloaded from the Scott Institute’s Research Repository on KiltHub at https://doi.org/10.1184/R1/27119169.v4.